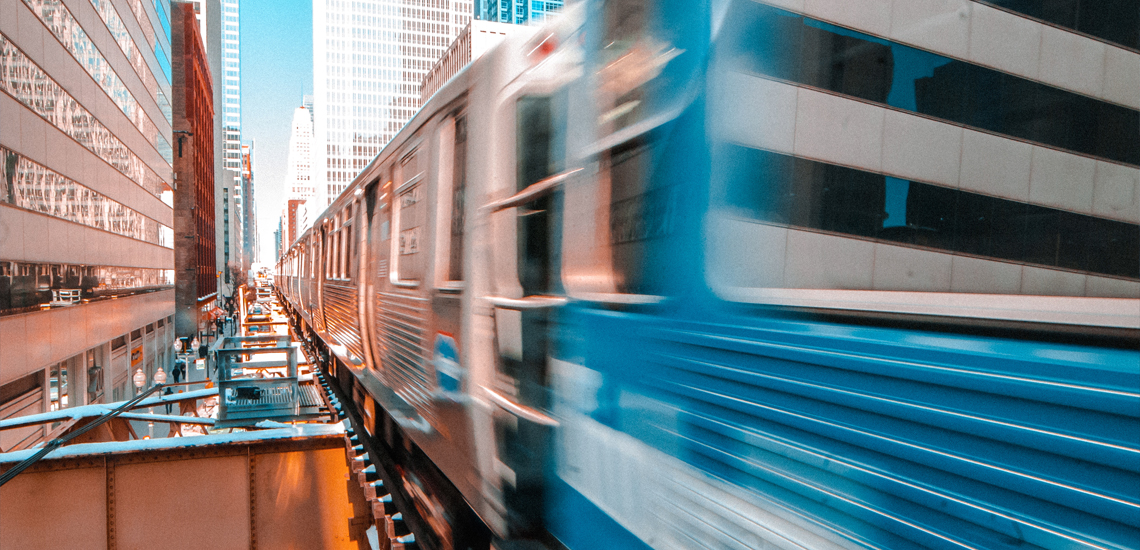
The One Brief has a New Home
Aon Insights has all the analysis you need to help you make better business decisions
You will be redirected to Aon.com in 15 seconds
Aon Insights has all the analysis you need to help you make better business decisions
You will be redirected to Aon.com in 15 seconds